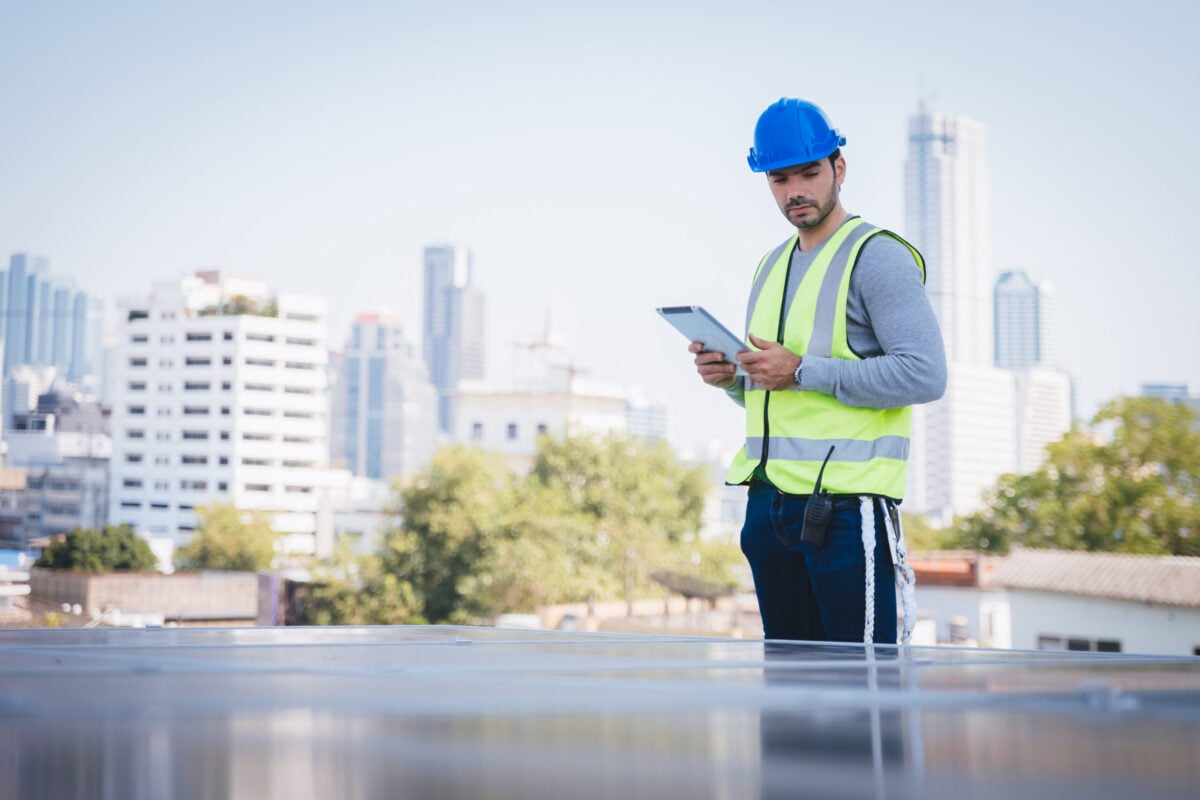
Commercial Roof Inspection Guide: Schedule, Document & Protect
07.15.2025
9 Min Read
A commercial roof represents one of your business’s most significant investments, yet many property owners overlook regular inspections until problems become costly emergencies. Your roof protects valuable equipment, inventory, and employees while maintaining the operational integrity of your facility. Understanding how to properly schedule, document, and maintain a commercial roof inspection can save thousands in repair costs and prevent devastating business interruptions.
This comprehensive guide will walk you through everything you need to know about commercial roof inspections, from establishing inspection schedules to working with qualified professionals who can keep your building protected year-round. Here’s what we’ll cover:
- Understanding commercial roof inspection basics
- 8 steps to a comprehensive commercial roof inspection
- Working with professional inspection services
- Common problems identified during inspections
🔎 Understanding Commercial Roof Inspection Basics

Commercial roofs face unique challenges compared to residential roofs, including heavy equipment installations, HVAC systems, satellite dishes, and constant foot traffic from maintenance crews. These stress points demand specialized attention during inspections. A thorough commercial roof inspection goes beyond the visible surface, evaluating membrane integrity, flashing conditions, drainage systems, penetration seals, and structural elements critical to your roof’s performance.
Weather exposure is another key factor, as commercial buildings often have large, low-slope surfaces that are more prone to water pooling, wind uplift, and thermal expansion issues. Regular inspections can catch these problems early, preserving your building’s integrity. Additionally, the inspection process is tailored to your specific roof type—whether it’s a built-up roof, modified bitumen system, single-ply membrane, or metal roofing—ensuring that the proper evaluation techniques and maintenance approaches are applied..
When to Schedule Your Commercial Roof Inspection
- Schedule bi-annual roof inspections in spring and fall for safe and thorough evaluations.
- Spring inspections address winter damage like ice dams, membrane splits, and drainage issues.
- Fall inspections prepare for winter by clearing debris, checking sealants, and securing loose materials.
- Request immediate inspections after severe weather events such as hailstorms, high winds, or heavy snow.
- Inspect roofs after building modifications like new HVAC installations or satellite dishes to ensure structural integrity.
- Increase inspection frequency for aging roofs: quarterly for those over 10 years old, annual for newer systems.
âś… 8 Steps to a Comprehensive Commercial Roof Inspection

Regular commercial roof inspections help prevent costly repairs and extend the lifespan of your roof. Identifying issues early ensures the safety of your building and avoids disruptions to your business operations.
1. Pre-Inspection Planning and Safety Setup
Professional inspectors begin every job with thorough preparation to ensure safety and accuracy. This starts with reviewing all relevant documentation, including building plans, previous inspection reports, and warranty documents, to gain a complete understanding of the roof’s design, materials, and repair history. Inspectors also consider the building’s age, climate conditions, and any reported issues to tailor their inspection approach. Safety is a top priority during this phase, so they establish comprehensive safety protocols, such as proper ladder placement, the use of fall protection equipment like harnesses and anchor points, and emergency response plans. Every detail is carefully considered to minimize risks for both workers and the building’s occupants.
2. Visual Ground-Level Assessment
Before stepping onto the roof, inspectors conduct a ground-level evaluation of the building’s exterior. They look for visible signs of wear and tear, such as missing shingles, cracked or damaged gutters, sagging eaves, or any structural irregularities that could indicate larger underlying issues. This initial assessment helps them establish a baseline of the roof’s condition and identify potential problem areas that require closer attention during the roof-level inspection. It also allows inspectors to note any environmental factors, such as overhanging trees, debris, or nearby structures, that could impact the roof’s performance over time.
3. Roof Surface and Membrane Evaluation
Once they safely access the roof, inspectors perform a detailed, systematic examination of the roof surface and membrane. They carefully check for signs of damage such as splits, punctures, blisters, or other issues that compromise the roof’s integrity and waterproofing ability. High-traffic areas, such as walkways and zones around rooftop equipment, are given extra attention since they are more prone to wear. Inspectors also examine seams, material transitions, and termination points where different materials meet, as these are common areas for leaks. Their goal is to catch even minor issues before they escalate into costly repairs or even roof replacements.
4. Flashing and Penetration Inspection
Flashing systems, which are critical for preventing water intrusion around edges and roof penetrations, are carefully inspected for durability and effectiveness. Inspectors visually examine all flashing materials, including metal and rubber, to detect signs of corrosion, separation, or improper installation. They conduct physical tests, such as checking the flexibility and adhesion of caulk lines, to ensure seals are intact and functioning properly. Special emphasis is placed on areas around chimneys, vents, skylights, and HVAC equipment, where flashing is often exposed to greater stress and wear. Proper overlap and alignment are also verified to ensure long-term water resistance.
5. Drainage System Assessment
An effective drainage system is essential to prevent water pooling, which can damage the roof and lead to leaks. Inspectors evaluate all drainage components, including gutters, downspouts, roof drains, and overflow systems, to ensure they are clear and functioning as intended. Minor blockages, such as leaves or debris, are cleared during the inspection to restore proper water flow. Inspectors also look for signs of standing water, rust, or sagging in the drainage infrastructure, which could indicate system inefficiencies. They identify areas where water is not draining correctly and recommend improvements to optimize water management.
6. Equipment and Structural Review
Rooftop equipment, such as HVAC units, satellite dishes, and solar panels, undergoes a thorough inspection to ensure proper installation and seal integrity. Inspectors check for loose or improperly mounted equipment that could damage the roof surface over time. They also evaluate seals around penetrations to ensure they are watertight and not contributing to leaks. Additionally, the roof’s structural components, including decking, support beams, and parapet walls, are inspected for signs of damage, deterioration, or structural strain. This review helps ensure that the roof can safely support its load and withstand environmental stresses.
7. Interior Inspection for Water Damage
A complete roof inspection includes assessing the building’s interior for signs of water infiltration. Inspectors look for active leaks, water stains, mold growth, or other moisture-related issues on ceilings, walls, and insulation. They use tools like moisture meters and thermal imaging cameras to detect hidden water damage that might not be immediately visible to the naked eye. By correlating interior issues with exterior findings, inspectors can identify the exact source of leaks and provide targeted repair recommendations. This step is crucial for preventing further damage and maintaining the building’s structural integrity.
8. Documentation and Reporting
After completing the inspection, professional roofers compile a detailed report that summarizes their findings. This report includes clear photographs of problem areas, descriptions of identified issues, and recommendations for repairs or maintenance. Each issue is prioritized based on severity, helping property owners plan their maintenance and repair schedules effectively. In addition, the report may include cost estimates and projected timelines for repairs, enabling better budgeting and decision-making. High-quality documentation ensures transparency and serves as a valuable reference for future inspections and maintenance efforts.
👨‍🔧 Working with Professional Inspection Services

Selecting qualified inspection professionals significantly impacts the value and accuracy of your roof evaluation. Look for companies with proper licensing, insurance coverage, and experience with your specific roof type and building style.
Certified Inspectors Ensure Quality
Certified inspectors bring specialized knowledge of commercial roofing systems, building codes, and industry best practices. Many roofing manufacturers require certified inspectors to maintain warranty coverage on their products.
The Importance of Local Expertise
Local expertise is crucial when choosing inspection services. Companies familiar with your area’s weather, building codes, and common roof issues provide more accurate assessments than contractors without regional experience.
Insurance Requirements for Inspectors
Insurance considerations play a role in selecting an inspector. Some insurance companies have preferred contractor lists or require specific certifications for claims processing. Ensure your chosen inspector meets these requirements before scheduling.
Balancing Cost and Thoroughness
When considering costs, aim to balance thoroughness with your budget. While detailed inspections may cost more upfront, they can identify issues early, saving money on expensive emergency repairs later.
❗️ Common Problems Identified During Inspections
Understanding typical commercial roof problems helps property owners recognize the value of professional inspections and prioritize maintenance efforts effectively.
Water Infiltration
Water infiltration is one of the most common and damaging issues inspectors find. Even small leaks can lead to interior damage, mold growth, and structural deterioration if not addressed. Regular inspections help detect problems early and prevent costly repairs.
Membrane Deterioration
All commercial roofing systems face membrane deterioration over time due to weather exposure and aging. Professional inspectors can differentiate between normal wear and accelerated damage caused by installation issues or material failure.
Drainage Problems
Debris buildup in gutters and drains often leads to drainage problems. Standing water speeds up membrane deterioration and adds structural stress, which can cause significant damage during heavy rain or snow.
Equipment-Related Damage
Roof materials are frequently damaged by HVAC contractors, satellite installers, or maintenance crews. Regular inspections catch these issues early, preventing water infiltration and protecting warranty coverage.
Wind Damage
Wind damage can be subtle but harmful, especially for single-ply membrane systems that depend on strong adhesion. Inspectors can spot loose materials that might tear away during future storms, ensuring the roof remains weather-resistant.
🏢 Trust the Roofing Experts for Your Commercial Inspection Needs
At Barkley-Jensen Roofing & Restoration, we take pride in being the trusted partner for all your commercial roofing needs. With years of experience, a customer-first approach, and a deep understanding of the unique challenges North Carolina properties face, our team delivers reliable, professional roof inspections that protect your investment.
From detailed evaluations and clear communication to working directly with insurance companies, we go above and beyond to ensure your roofing concerns are handled with care and expertise. Don’t leave your commercial property to chance—schedule your roof inspection with Barkley-Jensen Roofing & Restoration today and experience the peace of mind that comes with working with the best. Contact us now to get started!
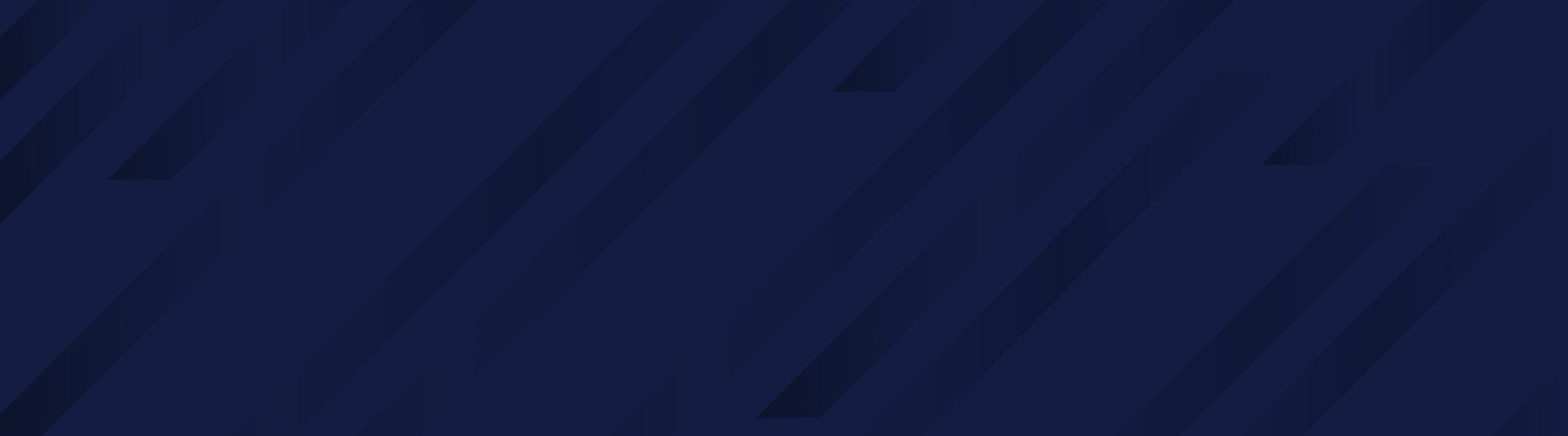
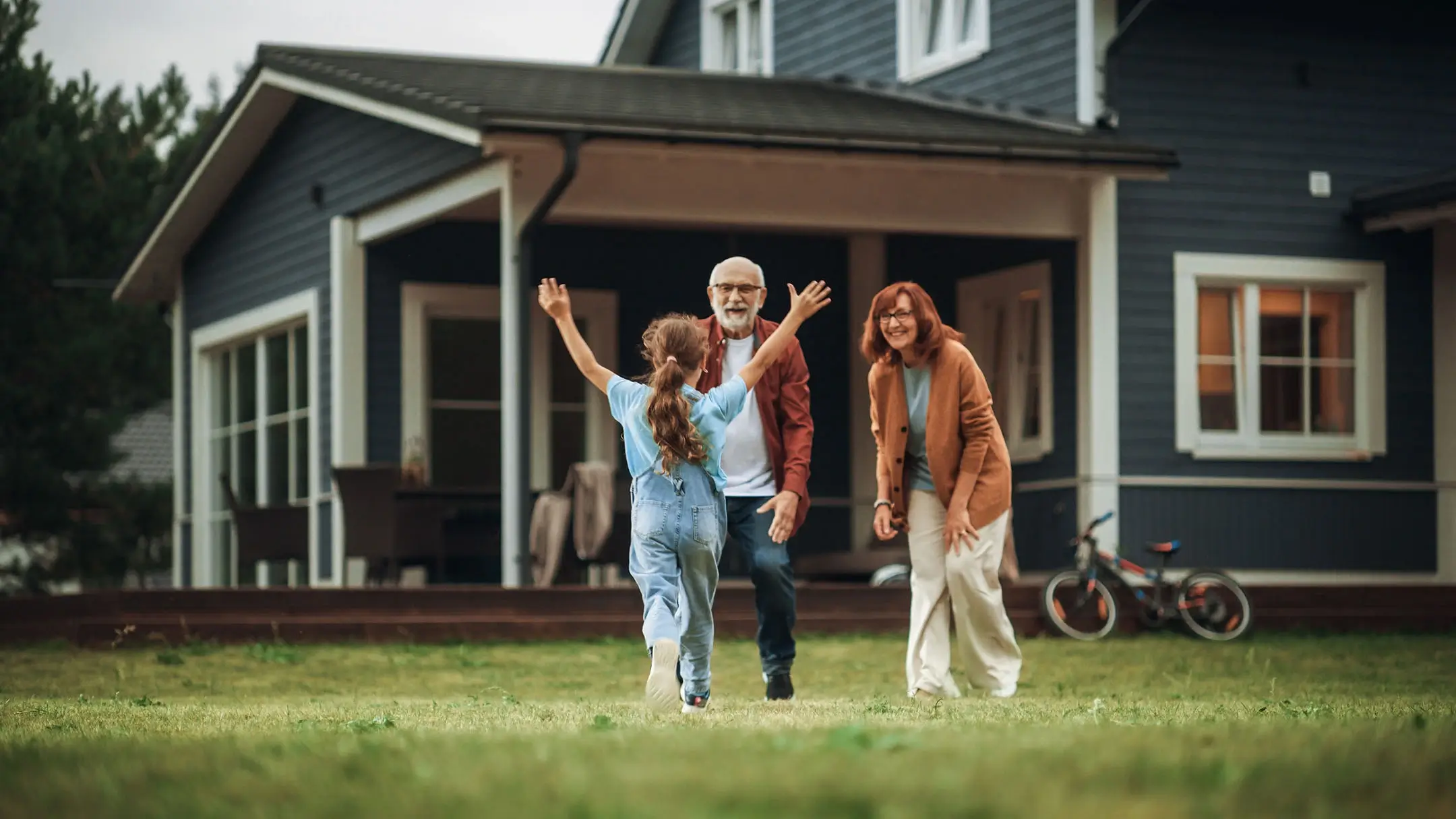